Flexitallic
Global Gasket Manufacturer
And Sealing Solutions
In Turkey

Flexitallic Global Gasket Manufacturer And Sealing Solutions In Turkey

About Us
FLEXITALLIC IS THE MARKET LEADER IN THE MANUFACTURE AND SUPPLY OF STATIC SEALING SOLUTIONS, DELIVERING HIGH QUALITY INDUSTRIAL GASKETS TO OUR TURKISH PARTNERS.
The Flexitallic Group is committed to its mission of “Making the world safer and cleaner through engineered sealing solutions”. Since the early days, we have been driven by the industry’s need for safe, effective sealing solutions for increasingly demanding applications.
We strive to achieve our mission by providing best-in-class sealing solutions, which allow our Turkish partners to operate their plants, complete projects, and start up from turnarounds safely and efficiently.
We channel the quality, innovation and experience of operating in diverse global markets to support Turkish industry while achieving our corporate goal, which is to provide the components required to achieve zero leaks on start-up and throughout the operating cycle.
Our industrial experience in Turkey includes petrochemical, power generation, nuclear power, beverages/distillation, geothermal plants and all other industry that requires high quality gaskets and sealing materials.
Products – Overview
Flexitallic remains at the forefront of developing sealing solutions for industries across the world. Available in Turkey, Flexitallic offers a wide range of high quality standard gaskets and customised sealing solutions that allow customers to operate their plants, complete projects and start up from shutdowns safely and efficiently. These products include:
- Velocity Washer™
- Thermiculite® – High Temperature Gasket Material
- Change™ Gasket – Heat Exchanger Gasket
- Sigma® PTFE Gaskets (Sigma 500, 511, 533, 588, 600 ePTFE, 850 ePTFE)
- Gasket Sheets, Flat Gaskets
- Corriculite® – Corrosion resistant material
- Flange Rescue Gasket® (FRG) – Corrosion Gasket
- Carrier Rings
- Seals/gaskets for high pressure, high temperature applications
- Seals/gaskets for heat exchangers, thermal cycling
- Seals/gaskets for galvanic and seawater corrosion
Velocity Washer™
In today’s world, speed, trust, savings and environmental impacts have become much more important.
With this unique product patented by Flexitallic, we offer great convenience, savings and confidence for flanged connections in your company – without any pre-preparation!
- The ultimate solution to the problem of what is often referred to as “stud wrapping” (galling) in the field
- Up to x30 times faster, safer and practical de-assembly
👇 With just a 90-second video, you can take a closer look at this product 👇
👇 With just a 90-second video, you can take a closer look at this product 👇
Thermiculite®
Process temperatures are rising and operators are looking to extend maintenance intervals. This requires gasket/sealing materials suitable for high temperature applications up to 1000°C which offer safe, long term reliability.
To address these issues, Flexitallic developed a material which has the same gasket sealing characteristics of graphite but the thermal resistance of mica – Thermiculite® high temperature gasket materials.
Suitable for use in critical sealing applications, Thermiculite® has a proven track record in fertilizer, nitric acid, ethylene, reformer and ammonia production, and is available as a gasket sheet, spiral wound gasket, kammprofile gasket, Change™ gasket and valve stem packing.
- High temperature gaskets/seals
- Fire-safe gasket/seals (API 6FB)
- Seals for high temperature packings/valves
- Seals for Molten Salt applications
- Gasket materials for Fuel Cell SOFC
- Gasket/Seals for Fertilizer production
- Cryogenic gasket/seal applications
Change™ Gasket
Due to the cyclical nature of temperature ranges handled by shell and tube heat exchangers, Change™ was originally developed by Flexitallic as a heat exchanger gasket, in response to customers’ long-term sealing problems.
Proven to outperform all other gaskets, Change™ has high recovery properties, without comprising tightness, which is essential in high temperature, thermal cycle applications.
Other typical Change™ applications include boiler manhole gaskets, damaged flanges, reactor seals (FCC, coker, hydrogenation, ethylene/fertilizer production).
- Gasket/Seal for Heat Exchangers
- Fire-safe gasket/seals (API 6FB)
- Gasket/Seals for thermal expansion/thermal cycling
- Gasket/Seals for low surface pressure
- Gasket/Seals for renewable energy
Enine Kesit
Sigma® (PTFE)
Utilising a unique manufacturing process exclusive to Flexitallic, SIGMA® represents the latest generation of multidirectional PTFE materials, which offer very high chemical resistance in processes ranging from cryogenic temperatures to 260°C.
All SIGMA® materials and PTFE filled seals/gaskets are FDA compliant, making them ideal for use in industries where product contamination is of concern.
Sigma 500 blue – PTFE modified with hollow glass microspheres. Enhanced compressibility for low bolt loads. Designed for glass pipelines, plastic and thin or distorted metal flanges.
Sigma 511 fawn – PTFE modified with silica filler. Suitable for strong acids (except hydrofluoric) and general chemicals.
Sigma 533 white – PTFE modified with barium sulphate. Suitable for strong alkalis and other general chemicals.
Sigma 588 sandwich – PTFE material with low stress characteristics, ideal for low load sealing in damaged flange surfaces. Used in both concentrated acid and alkali service.
Sigma 600 white – PTFE material with low stress characteristics and high compressibility for ultra low bolt loads; plastic and glass lined equipment. Universal material suitable across a wide range of chemical media.
Sigma 800 ePTFE – Expanded PTFE sheet material with enhanced low stress sealing characteristics and improved blow-out resistance and is suitable for sealing most chemicals across the pH range.
- FDA compliant seals/gaskets
- Gasket/Seals for chemical, pharmaceutical, food
- Gasket/Seals for cryogenic applications
- Reactor Seals/Gaskets
- Gasket/Seals for GFK Flange
- Teflon Seals/Gaskets
Corriculite®
Corrosion often remains undetected, be it in exposed pipework or less visible configurations such as buried or subsea pipework, or because of infrequent periods of maintenance.
Flexitallic has responded to the challenge confronting key sectors such as oil and gas, petrochemicals, power generation and refining, to develop the next generation of corrosion prevention materials – Corriculite®. The key requirement is to extend equipment life by minimising or eradicating the threat of corrosion.
Conventional graphite gaskets for instance, are known to promote corrosion of flanges due to graphite’s electrical conductivity and position in the
An inert, non-conductive filler material, it is used in a range of corrosion sensitive areas, including seawater, hydrocarbon processing and hydrogen process, across several sectors including marine and chemical processing. It offers significantly improved sealing characteristics compared to traditional sealing materials and is also fire safe to API 6FB.
- Gaskets/Seals for Corrosion
- Gaskets/Seals for seawater applications (fire fighting pipelines)
- Gaskets/Seals for Hydrocarbon service
- Fire-safe gasket/seals (API 6FB)
- Graphite gasket alternative – Corrosion
Flange Rescue Gasket (FRG)
Developed in direct response to the oil and gas industry’s requirement for effective closure on damaged flange faces, with additional corrosion inhibiting properties, the FRG gasket is now helping to mitigate corrosion problems throughout industry.
The FRG can be used to seal on damaged flange faces and is useful for remedial repairs on corroded equipment AND as a preventative solution on new equipment to prolong its life and avoid costly shutdowns.
- Gasket/Seals for corrosion
- Gasket/Seals for damaged flange faces
- Gasket/Seals for galvanic corrosion
- Gaskets/Seals for seawater applications
- Gaskets/Seals for Hydrocarbon service
- Fire-safe gasket/seals (API 6FB)
Flange Rescue Gasket – original
- Restructured Sigma® PTFE bonded to high integrity metal core
- Leak free seal and below out resistance
- Bright and easy identifiable for inspection
- Corrosion resistant coating
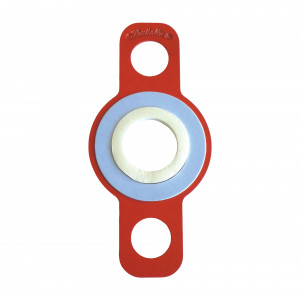
Fire Safe
- Thermiculite® high temperature insulating corrosion resistant material
- Certified to API 6FB for fire-safe applications
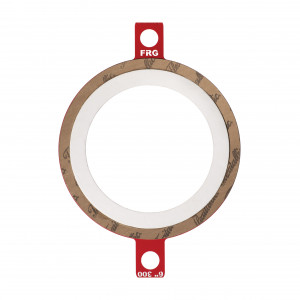
Cryogenic
- Aluminium core as standard
- Core material can be adapted to match the flange materials
- PTFE ring performs in temperatures from cryogenic to 260°C
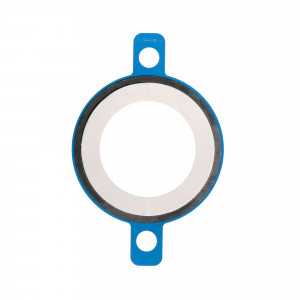
FRG Subsea
- Easy subsea installation with integrated removable handle
- Use to connect RTJ & RF Flanges
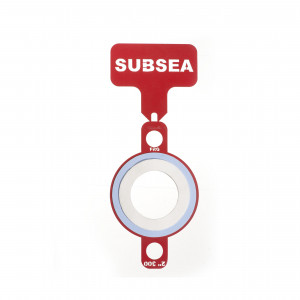
Carrier Rings
The Flexitallic Carrier Ring has been successfully used in sealing problematic flanges and vessels in the nuclear, power and petrochemical industries.
The major benefits of using Carrier Ring assembly are due to the double spiral wound gasket. This results in a very high recovery gasket, ensuring that bolt load is maintained on the sealing elements when high pressure/temperature cycling occurs in service.
Typical applications include heat exchangers, HP Heaters, Fossil Fired Generators, Steam Service and Catalytic Crackers.
The Carrier Ring can be considered as an alternative product to Ring Type Joints (RTJ’s.)
- Solid Metal Gasket Ring
- Metallic Gaskets/Seals for high pressure
- Metallic Gaskets/Seals for high recovery
- Metallic Gaskets/Seals for heat exchangers
- Metallic Gaskets/Seals for high temperature
Joint Integrity Services
Our team of application engineers understand that the use of high quality seals/gaskets are not a guarantee of sealing success. As a result, Flexitallic application engineering offer a range of Joint Integrity and Technical Services that are designed to complement and enhance Flexitallic’s product offering.
Allowing customers to operate their plants, complete projects and start up from turnarounds safely and efficiently. Our goal is to help customers achieve leak free start-up and operation within the scheduled maintenance cycle.
- Shutdown support
- 13555 Sealing material characteristic values
- EN 1591 calculation for gaskets
- Gasket installation training – 1591-4
- Gaskets to VDI 2290, VDI 2240, TA Luft
- Gasket assembly support
- Application consulting and design
- Research and Development Lab (R&D)
- AMTEC Test benches
- AMTEC High Temperature testing